Enhanced digital systems in O&M can further reduce the cost of offshore wind energy –
Enhanced digital systems in O&M can further reduce the cost of offshore wind energy –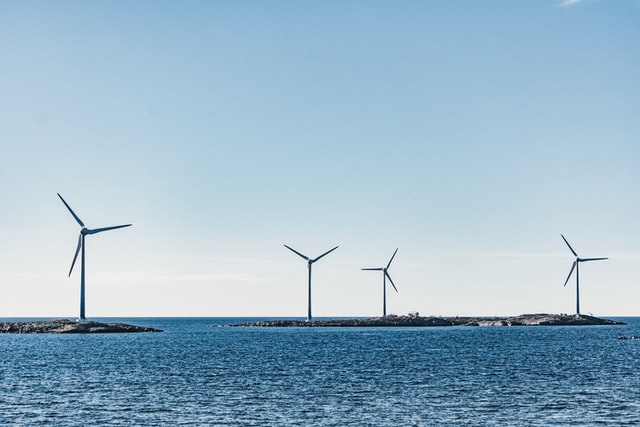
In just under a decade, offshore wind’s levelized cost of energy (LCOE) has been halved from ~£150/MWh in Europe. Yet, how much lower can it be reduced? Our latest analysis reveals significant room for further improvement, particularly in operations and maintenance (O&M). Reducing offshore visits, ensuring the right workers have the right materials and applying remote, autonomous and automated technologies are collectively the key to lower energy costs in wind’s future.
To delve deeper into the current digital landscape and explore how enhanced digital systems can deliver more value from O&M and enable lower LCOE, Accenture and The Offshore Renewable Energy (ORE) Catapult, the U.K.’s leading technology innovation and research center for offshore renewable energy, interviewed 11 leading wind players with an emphasis on offshore.
To support such improvements in O&M, it’s crucial for wind operators to first bear in mind that there is no single application that covers all process areas. Larger players have developed or are developing in-house capabilities using big data and advanced analytics to raise performance levels across multiple technology types. This requires heavy investment in strategic platforms, favoring custom solutions, rather than off-the-shelf applications.
Indeed, this is in line with our study, which revealed operators use diverse solutions including custom applications and packages. No standard architecture or service provider is emerging to lead the pack right now, so most wind operators use a hybrid system, with on-premise supervisory control and data acquisition (SCADA) systems and cloud services for data visualization. There was also strong focus among study participants on additional monitoring systems such as strain gauges, gearbox monitoring, oil analyses and misalignments on yaw and blade pitching systems.
So, with all that in mind, what are the challenges wind operators face, when trying to bolster O&M value from data and the application landscape itself? These are manifold:
- Connectivity: Breaks in connectivity between the wind farms and the operations center which impact health and safety, work execution, the quality of data collected and cybersecurity.
- Standardization of alarms/faults: Lack of consistency of alarms, tags, faults across original equipment manufacturers (OEMs), asset models, reports and benchmarking.
- Calibration of equipment: Lack of frequent calibration of sensors and alarms, or defined methods and processes in place to measure, analyze and report accuracy.
- Use of sensors: Lack of overall understanding of the importance of some sensors, resulting in sensors not being used to their full potential, or combined with other data to predict and assess asset health.
- Access to data: Inability to obtain data from the OEM, and a lack of clarity on the rights to data.
- Volume of data: When data is available to transfer between OEM and owner at the end of the warranty period, the owner can be overwhelmed by the data volume and may lack the capability to generate meaningful insights from the data.
- Value unclear: Lack of awareness of the benefits of digital enablers, and tools not being used to their full capability.
In response to those challenges, we identified six O&M use cases which, enabled by digital, could drive significant performance improvements and reduce LCOE for wind operators: alerts, alarms, warnings and faults; troubleshooting and minor corrective maintenance; failure prediction and major component replacement; scheduled maintenance; wind power curve analysis and production losses; and production forecasting.
When asked about the impact of enhanced digital systems on these key O&M use cases, study participants suggested that the most significant improvement opportunities were in four of those areas:
Alerts, alarms, warnings and faults. This area was assessed by 73% of participants as a significant opportunity for improvement from better digital systems.Currently, a lack of standardization of alarms and significant differences across OEMs and turbine platforms presents a significant barrier to innovation and challenges with scaling beyond a single wind farm. Automating manual processes can have a significant impact on time spent on alarm classification identification for larger sites. Integration between new and legacy systems is also key but currently an obstacle. More advanced operators are integrating advanced monitoring, classifications and recommendation for common failure modes. Some packages also support linking alarms and alerts to standards, avoiding the need and knowledge required to do it manually.
Troubleshooting and minor corrective maintenance. More than half (55%) of participants see this as a significant opportunity for digital impact. Inconsistencies between the input of alerts, alarms and alignment to fault hierarchies currently cause issues with scaling troubleshooting approaches beyond individual wind farms. Furthermore, issues with connectivity to the wind farms can cause problems with digital systems in the field, making access to real-time data and expert advice difficult. As such, there is a need to expand the use of communication and collaboration platforms that combine workplace chat, video meetings, file storage, application integration and mobility for connected worker elements and access to offline manuals.
Failure prediction and major component repair. This area was assessed by all participants as a significant opportunity for digital impact. Right now, failure prediction appears limited to vibration analysis and temperature trending on the drive-train components, as they are the most expensive to replace. However, there is appetite to apply similar techniques on smaller components that fail more often, such as pitch systems and power electronics. Additionally, while some failure prediction analysis is outsourced as part of procured condition-monitoring systems, most of our respondents are very interested in doing much more of this in-house. More forward-thinking operators are also looking to build or buy advanced monitoring applications with automated fault classification and recommendation engines for common failure modes.
Production forecasting. Almost two thirds (64%) of participants see this area as a significant opportunity for improvement from enhanced digital systems. It will certainly be more important in the future, when offshore wind generation may be subject to widespread curtailment requests or participate in balancing markets. Currently, there is a siloed approach to production forecasting by operators and energy management teams and updating production forecasting varies greatly between companies—from monthly to once every few years. Indeed, our analysis revealed only 55% of the respondents currently update their pre-construction production forecasting. While substantial, the benefits of regularly updates are not fully appreciated, and some respondents believe that they do not outweigh the cost of doing so.
While improvement in all these areas can help operators avoid or at least reduce the number of maintenance visits, and improve the efficiency and effectiveness of those trips offshore, the value of building an appropriate foundation and operating model to leverage digital more broadly should also not be underestimated. These opportunities include installing Wi-Fi and 5G to improve connectivity between wind farms and the operations center, investing in domain and analytics expertise to predict asset health threats, bolstering end-user centricity and using an optimal change-management approach.
Wind operators can no longer delay action. ORE Catapult estimates that O&M can now constitute approximately 40% of offshore wind LCOE, but by focusing on installing enhanced digital capabilities in the most relevant areas, significant improvements can be delivered that will drive down the cost of energy. Critical to this endeavor is a greater focus on cloud platforms and digital application capabilities for O&M processes to reduce costs, while improving production.